So Transparent: Crystal Palace reloaded Brad Turner. November 20, 2015.
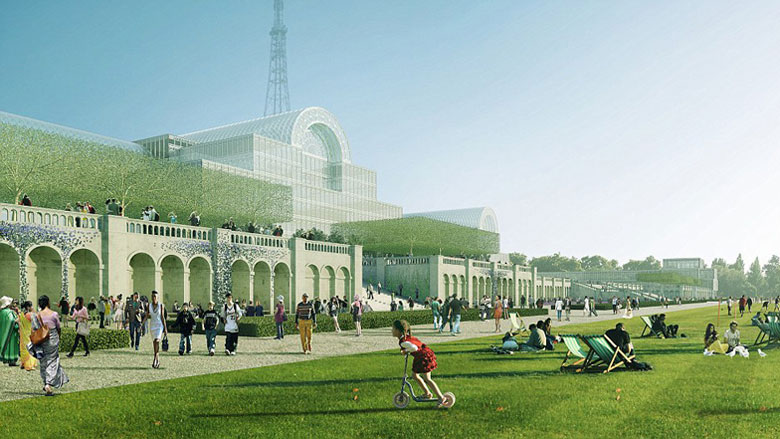
Zaha Hadid, Grimshaw and Rogers, Stirk + Harbour are among the shortlisted architects recently selected to put forward designs to recreate London’s iconic Crystal Palace. In this article, originally published on Architonic, Materials Council explores the materials and technologies a modern day interpretation of the Crystal Palace could make use of.
Last October a Chinese developer announced their intention to rebuild the iconic Crystal Palace, originally built for Britain’s 1851 Great Exhibition – an international expo of industry and culture from the country’s vast empire and beyond. Initially billed as a faithful reconstruction of the original building, the Zhong Rong Group, in the face of criticism from both the public and the architectural community, later tendered a competition to create a ‘spiritual successor’.
In advance of the winner being announced, Materials Council decided to explore how the requirements specified by the original design committee, the original building’s design innovations, and contemporary glazing and material technologies could inform a modern-day interpretation of the Crystal Palace.
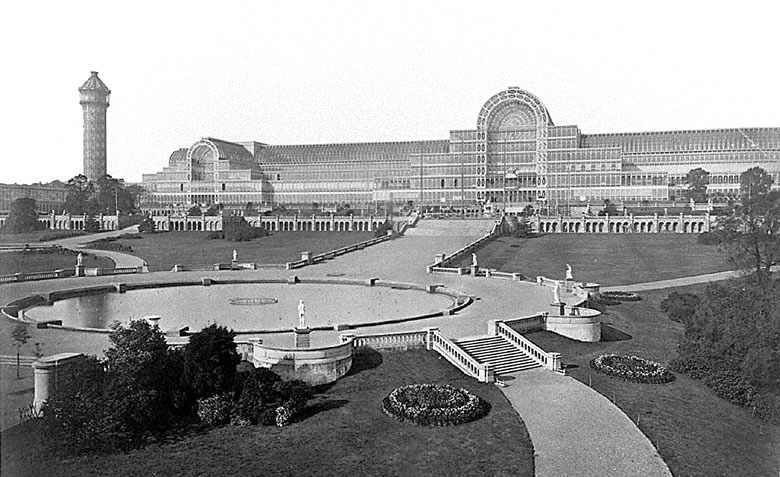
The spirit of Crystal Palace
The original Crystal Palace, erected in Hyde Park, London, was a radical architectural advancement. It was designed by Joseph Paxton after an unsuccessful competition to find a suitable design satisfying the building committee’s key specifications. They stipulated that the building be:
• temporary
• simple
• as cheap as possible
• economical to build in less than a year before the already scheduled exhibition
It has been regarded as marking the start of architectural modernity, trumpeted by Le Corbusier as the ‘herald of a new age’, and is arguably the progenitor of the ‘High Tech’ architecture of Norman Foster, Richard Rogers, et al.
The Crystal Palace was a paradigm shift. Not only in what an architectural space could be but also the design concepts, engineering and construction processes required to successfully realise a building of an entirely new materiality and subject to unprecedented constraints.
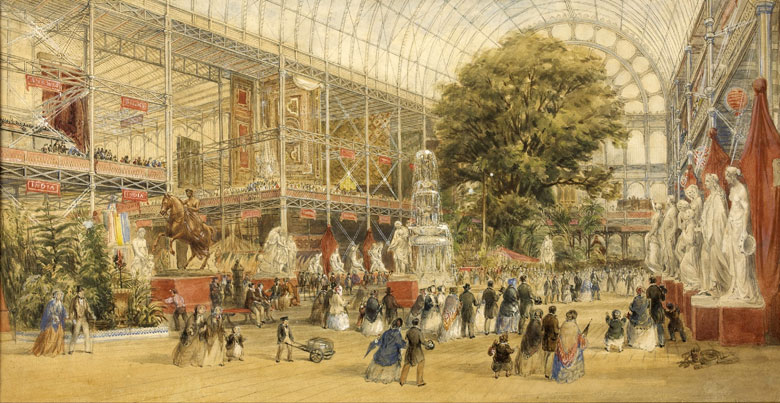
After its initial six-month life in Hyde Park, the original Crystal Palace was dismantled and relocated to its eventual home in Sydenham Hill, South London. Here, an expanded design of the Crystal Palace was rebuilt using most of the original components as the basis of a larger, but quite different in form, incarnation, which stood for 82 years before succumbing to fire. It is this location, which, in the interim, has lent its name to the surrounding neighbourhood, that the Zhong Rong Group controversially intends to redevelop.
To protect the development of the site a 1990 Act of Parliament, rather vaguely, insists that any building placed there should ‘contain a predominance of glass and metal or similar materials and that the building should reflect the spirit of the original Crystal Palace’. Paxton’s pioneering design concepts and construction principles are illustrated in the competition brief as the key aspect of this ‘spirit’.
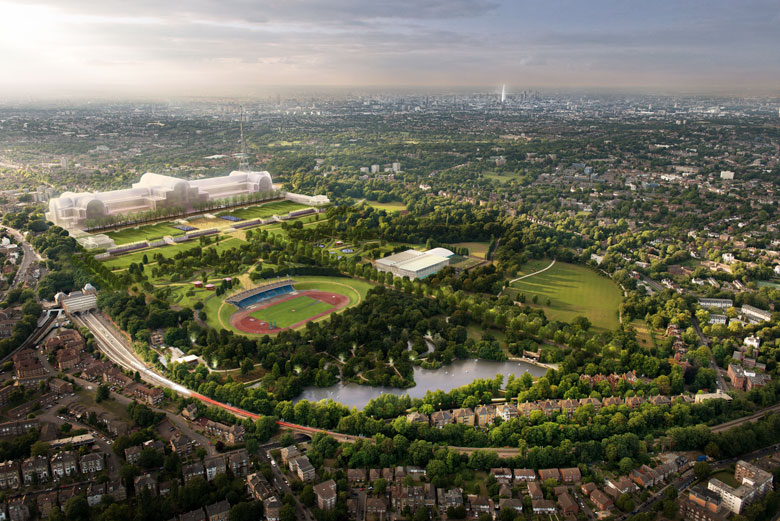
Zaha Hadid & Anish Kapoor, Grimshaw, Haworth Tompkins, Marks Barfield, David Chipperfield and Rogers Stirk Harbour & Partners make up the shortlist of architects announced at the end of February. Up to three teams from the shortlist will be invited to submit initial design concepts with the winner eventually being announced in the summer.
Modular, prefabricated system
Paxton expanded upon previous experimentations in the construction of glasshouses to propose a design that surpassed the building committee’s specifications. It was vastly cheaper and quicker to construct than any other proposal or form of building of comparable size, going from sketch to completed building in less than nine months.
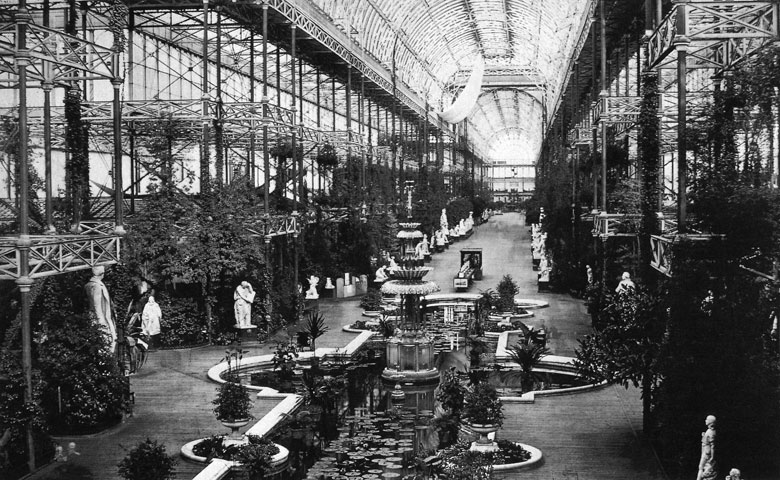
Based around the dimensions of the largest available glass sheet, Paxton created an incredibly flexible, modular, gridded design that could form a variety of spaces. It even allowed him to alter the design during the course of the construction.
The structure comprised repeating modules made from a system of prefabricated cast-iron elements, exploiting for the first time the benefits of prefab construction. These cast-iron parts were incredibly easy, fast and economical to manufacture on a large scale. Produced under controlled conditions, accuracy and quality was ensured.
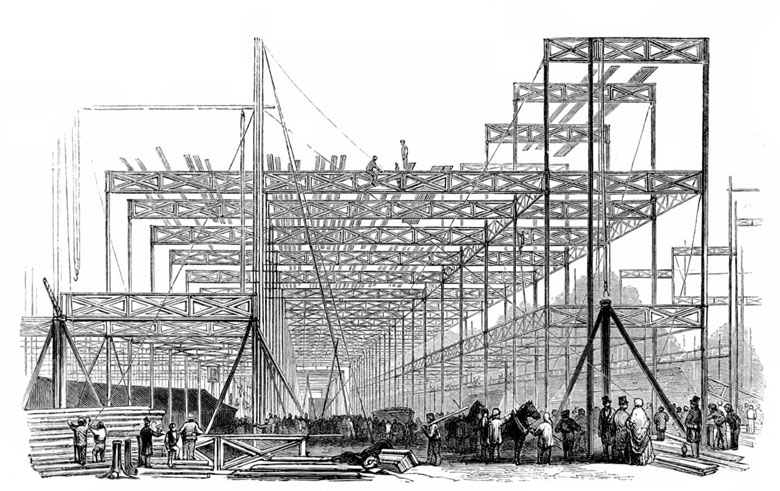
Construction was also exceedingly quick. The building could be assembled section-by-section as parts arrived on site, with some sections standing within 18 hours of leaving the factory. This enabled the majority of the building to be completed in just five months.
While the use of prefabricated steel members and other components are now commonplace, processes are still being refined to maximise the benefits afforded. The construction of Rogers Stirk + Harbour‘s Leadenhall building breaks new ground in this regard.
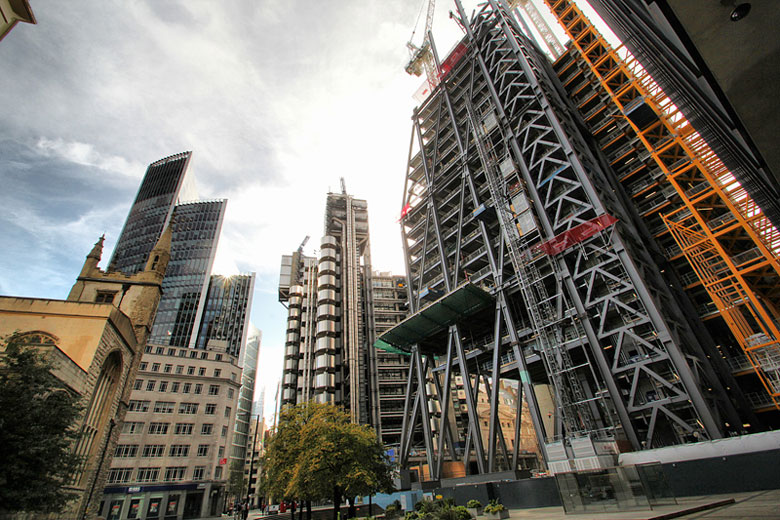
The high-profile location, tight footprint and narrow streets of the site present considerable challenges to construction. As a result 85% of the building’s built value consists of prefabricated and off-site manufactured elements. Instead of using a central concrete core the structure is primarily provided by a steel perimeter mega-frame. The services tower of the building comprises prefabricated structural steel ‘tables’ preassembled off-site with mechanical and electrical plant and precast concrete slabs.
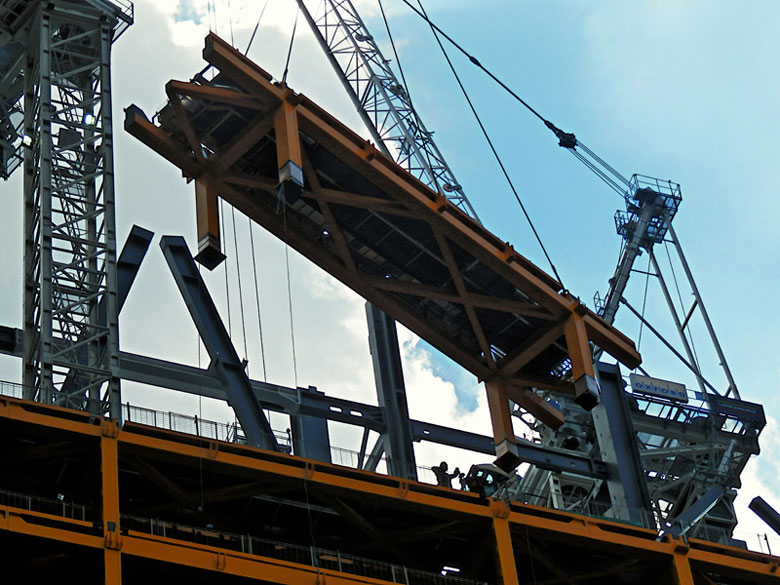
The project has also pioneered the use of radio frequency identification (RFID) software to track building components through manufacture, delivery and installation. In conjunction with BIM the contractors have refined the just-in-time assembly process, enabling them to anticipate delays downstream and take preventative action.
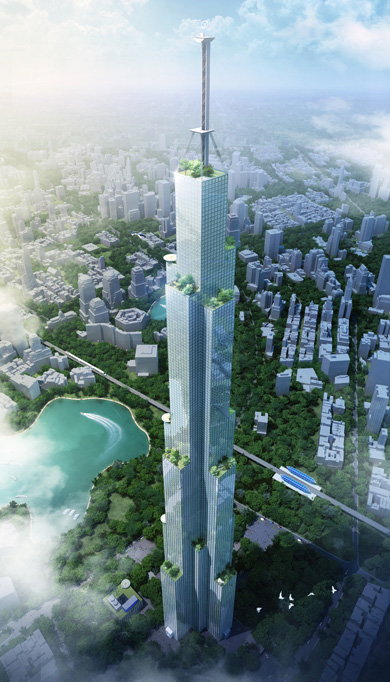
This has enabled construction to minimise disruption for neighbours, reduce noise, increase on-site safety, speed up erection and reduce the required on-site workforce by around 40% compared to traditional builds.
The Broad Group of China believe their 95% prefabricated modular technology will allow them to create the world’s tallest building in only nine months, including just three months onsite. Construction will reportedly be one tenth the cost of the current tallest building, the Burj Khalifa.
The boundaries of glass
The Crystal Palace was, at the time, the largest glazed building in the world. Today many of our largest buildings are covered in a glazed skin but few push the envelope of what is now possible at the extreme end of glass manufacturing and technology.
Paxton based his Crystal Palace design around the dimensions of the largest available standard sheet of glass. At the time a pane of 0.2 x 1.2 metres, produced using the recently invented cast glass plate manufacturing process. This meant the facade could be glazed astonishingly quickly. Using the standard panes without trimming, a team of 80 glaziers installed them at a rate of 18,000 panes per week.
Today the largest sheets of float glass offered by manufacturers measure 3.3 metres wide as standard and at most 18 metres long, though some manufacturers can produce mega sheets at 4 metres wide; their dimensions dictated by the existing machinery used in their manufacture and the logistics involved. Yet rarely, if ever, will you see glass of this scale employed across the facade of a building. Their cost and the sheer practicalities of transporting and installing such sheets being wildly prohibitive.

However, there are examples of smaller structures that have utilised mega sheets of glass that hint at what an interpretation of Crystal Palace free of these constraints could look like.
In their designs for Apple stores around the world, the partnership of specialist glass fabricators Seele Sedak and facade and glass engineers Eckersley O’Callaghan has pushed the boundaries of what is possible with glass production and construction at the extreme end of the spectrum. And in Apple they have a more than willing patron and instigator.
The redesign of the iconic glass cube entrance to the 5th Avenue Apple Store in New York reduced the number of glass sheets per face down from 18 to just three panes of five-ply, ionoplast-laminated safety glass measuring 10.3 x 3.3 metres. Held together by titanium fixings, fitted into the glass panels during the lamination process making them almost completely concealed, the structure is virtually entirely glass.

Apple’s determination to use, at 13 metres, the world’s largest curved glass sheets for the entrance to their Shanghai store even propelled them to develop a new production facility with their local Chinese glass fabricators that could match their exacting demands. Curved panels of a similar scale are expected to be used on an unprecedented scale at the new Apple campus in Cupertino, designed by Foster + Partners architects, glazing the entire facade.
An interesting development in architectural glass is the new availability of Corning’s Gorilla Glass; ubiquitous in the screen technology of almost every electronic device we prod throughout the day.
Corning’s unique ‘fusion-draw’ glass-manufacturing process and chemical-strengthening techniques produce an incredibly strong, thin, damage-resistant yet flexible glass with excellent surface quality and optical clarity. Its greater strength allows it to be used in architectural applications in much smaller thicknesses but with the same strength and stiffness. However, its current cost again limits its implementation.
Unfortunately, Corning’s exploration of architectural applications has so far not gone much further than turning every surface into a touch screen. Envisioning an unpleasantly greasy future of universally smudged and streaked interiors.
So while extreme structural glass designs are possible they’re unfortunately not reasonably practical.
Another issue with using glass in this manner is thermal performance, due to its poor insulation and issues of solar control. To use insulated glazed units (IGU) or highly reflective solar coatings would defeat the aesthetic purity these minimal, transparent glass structures are designed to achieve in the first place.
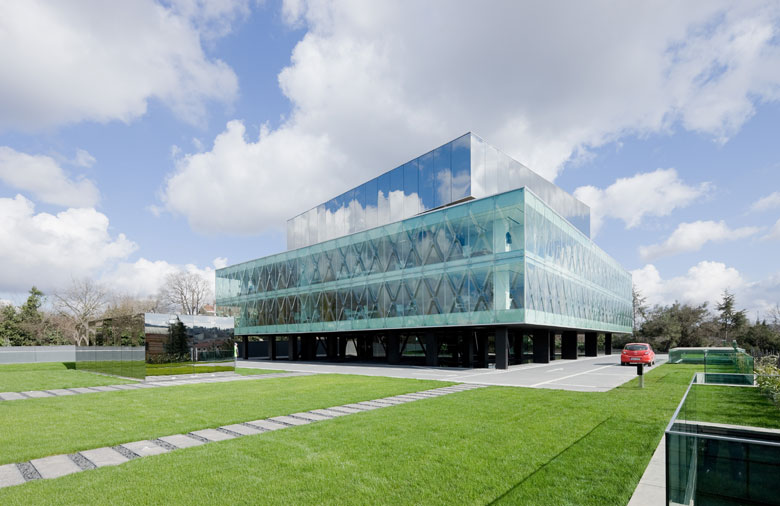
Perhaps REX‘s approach to the glazing of the Vakko Fashion Center in Istanbul offers a compromise of structural performance, insulation performance and visual clarity. By using a slumping glass manufacturing process the architects formed an X into one glass face of an IGU. The result was a much stronger and stiffer IGU, eliminating the need for additional structural columns around the perimeter of the building.
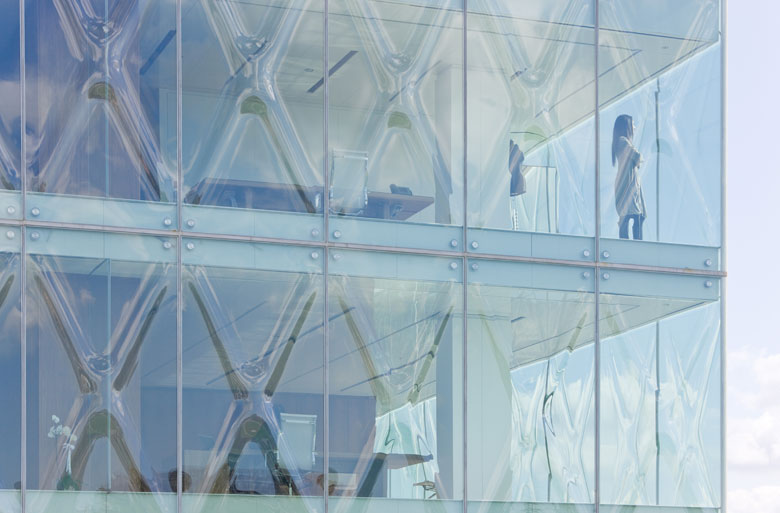
Low-cost, large span
Looking beyond glass, if we are to take inspiration from the intentions of the original Crystal Palace we should look to the design of structures such as the biomes of the Eden Project by Grimshaw and the Millennium Dome by Richard Rogers Partnership. Tellingly, Tim Smit, co-founder of the Eden Project, has been appointed to the advisory board assigned to develop the design principles for the building and both Rogers and Grimshaw have been shortlisted.
The Millennium Dome and the ‘Millennium Experience’ housed within were undoubtedly inspired by the Great Exhibition itself. While the result was not the public and critical success of the Crystal Palace (proving more successful in its current incarnation as a multi-purpose entertainment venue) many of the building constraints were similar.
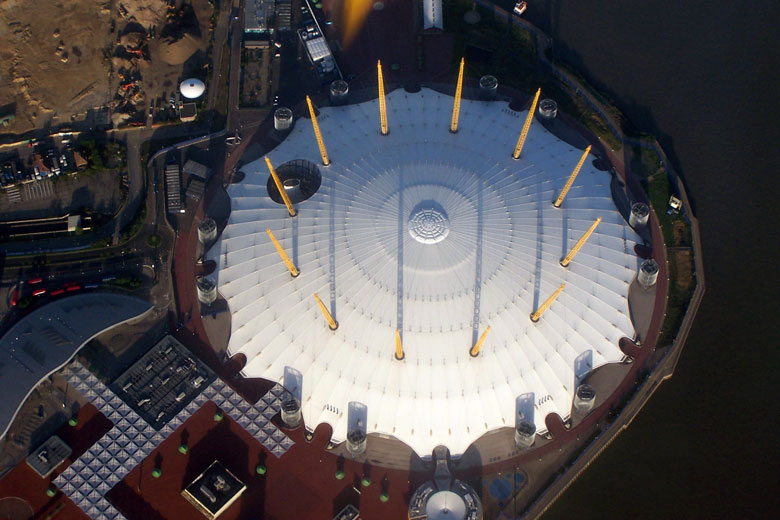
The Millennium Dome was delivered within fifteen months and under its already remarkably inexpensive budget for a structure of its scale. The architects achieved this by utilising standardised components and employing the largest ever span of Teflon-coated, glass-fibre tensile membrane. This was supported by a net structure of 70 kilometres of high-strength steel cable suspended from a series of twelve 100-metre steel masts. The result is either the most permanent tent ever or the most impermanent building.
The biomes of the Eden Project share even more DNA with Paxton’s Crystal Palace, bringing many of his design concepts full circle.
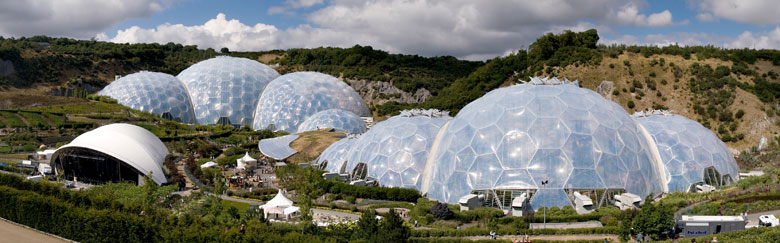
As Paxton adapted his design to the site-specific demands of Hyde Park, adding the barrel-vaulted roof to accommodate the existing trees of Hyde Park, the geodesic domes of the Eden biomes were also in part chosen for this ability; geodesic hexagons at the interface with the ground could be added or removed allowing the domes to easily adapt and follow the uneven and ever-shifting ground profile of the quarry bed they were to be situated in.
The first use of lattice beams in the structure of Crystal Palace enabled Paxton to create large, open exhibition spaces uninterrupted by structural columns. This allowed daylight to penetrate throughout the building as never experienced before.
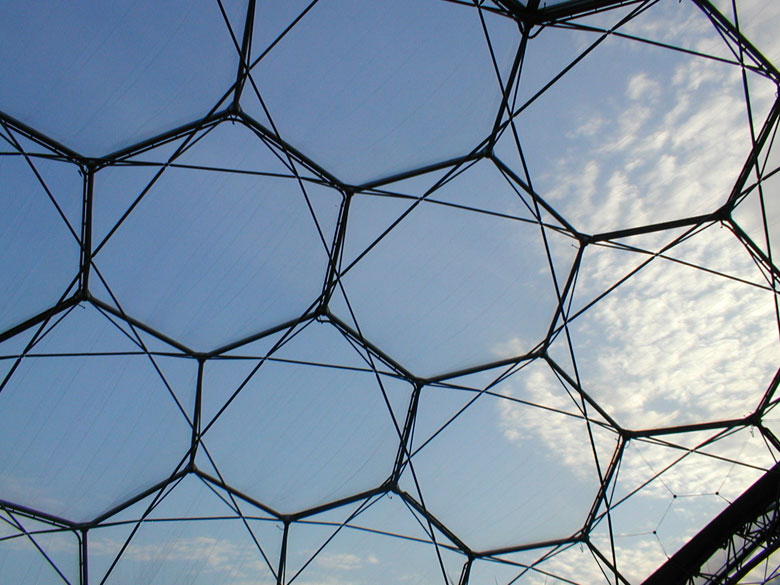
The domes of Eden employ a highly efficient and strong ‘hex-tri-hex’ structure, assembled from a network of prefabricated standardised aluminium or galvanised steel components. This forms a completely self-supporting shell spanning the 240 metres of the largest biome without any internal support, creating the undisturbed tropical ecosystem within.
The structure is clad with the copolymer ethylene tetrafluoroethylene (ETFE). At 1% the weight of glass, ETFE can span up to six or seven times the distance between supports when used for a roof. This ETFE cladding takes the form of inflated triple-layer pillows, which provide excellent light transmission and insulation (achieving better U values than triple-glazing when used horizontally). Complete ETFE cladding systems also have a carbon footprint that is approximately 80 times lower than comparable transparent systems and can cost between 24-70% less than glazing when installed.
Comfortable environments
By translating ideas explored previously in the design and construction of glasshouses to create functioning exhibition spaces for people, Paxton pioneered solutions for design problems that had not yet been encountered.
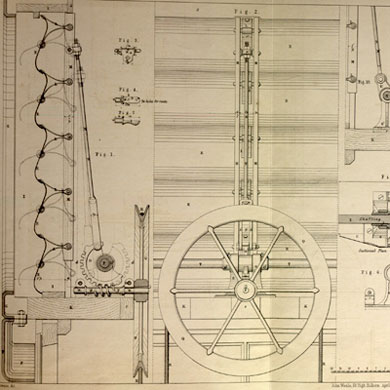
The expansive skin of glass permitted excessive levels of light and heat radiation into the building’s interior. When combined with the radiated heat from the throng of crowds and the inability to escape direct sunlight when viewing the exhibits, unbearably warm and uncomfortable conditions were created.
To mitigate these issues Paxton retrofitted exterior canvas shades to the roof of the building to reduce solar gain and diffuse the light penetrating the exhibition space. By spraying water onto these canvas shades they also worked as an ingenious yet simple evaporative cooling system, drawing heat away from the building. Paxton also employed a passive ventilation system to cool the interior through the stack effect. Utilising mechanically operated louvres situated in the glazed walls, the shaded, cooler air from the bottom of the building was sucked up through the gaps in the floorboards and forcing the upper warm air out through the open louvres.
ZhongRong Group’s competition brief acknowledges the difficulty in balancing the desire for a translucent skin with creating comfortable interior environments for the users. It indicates that they wish to achieve this by employing more intelligent solutions to reduce the operational energy of the building, specifying an active facade to minimise the need for powered heating, ventilation and air-conditioning.
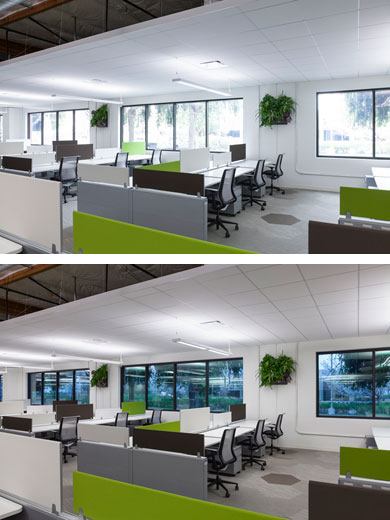
A range of recently developed adaptive technologies could be looked at to supplement or replace the established, fixed techniques of solar control such as shading, coating or fritting. All methods of solar control impact to some degree the optical transparency of an envelope but through the use of an active facade this can be intelligently managed to only occur on localised areas of the facade as required. In this way the sun can play a part in creating the changing appearance of the building throughout the day.
‘Smart glass’ technologies, such as View‘s electrochromic glass, use a small electrical current to alter the orientation of pigments or particles suspended in a thin film, changing the tint and the amount of light admitted in response to feedback from internal or external sensors or manual controls. This reduces the need for additional shading, preserves views, minimises glare, reduces the heating and cooling needs and also protects objects in the interior from UV damage. The change in translucency can be achieved through a darkening tint, a milky-white opacity change or, more recently developed, increased reflectivity.
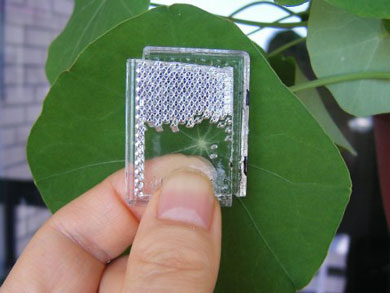
An exciting low-tech ‘smart glass’ is the SunValve, invented by Norwegian Kim Øyhus. Using two sheets of transparent plastic retroreflective prisms (as found in bike reflectors) separated by an air gap, the SunValve can switch between opaque and transparent states by filling the gap with a clear liquid.
When empty, the valve is closed and the prisms reflect light and heat back towards the source, giving the material an extraordinary glowing appearance. When filled with liquid the window becomes transparent. The SunValve is a simple, mechanical, low-cost alternative and has been released by Øyhus without patent to encourage its adoption, though has so far been overlooked and remains uncommercialised.
Adaptive fritting technologies, as explored by Chuck Hoberman and the Adaptive Building Initiative, can also be controlled to permit more or less direct light as required. Graphic patterns printed onto layers of glass or plastic move over each other, modulating transparency and controlling the transmitted light, solar gain, privacy, and views. This can also be achieved by ETFE pillows within a typical cladding installation. By altering the pressure between two printed foils in a pillow, the alignment of the printed designs, and therefore the amount of light permitted, is altered.
Adaptive shading acts similarly, controlling light and solar gain by altering the admission of direct light to the interior, but can also be used to control ventilation and airflow, similar to Paxton’s louvres. Though it does present a more permanent, solid visual screen.
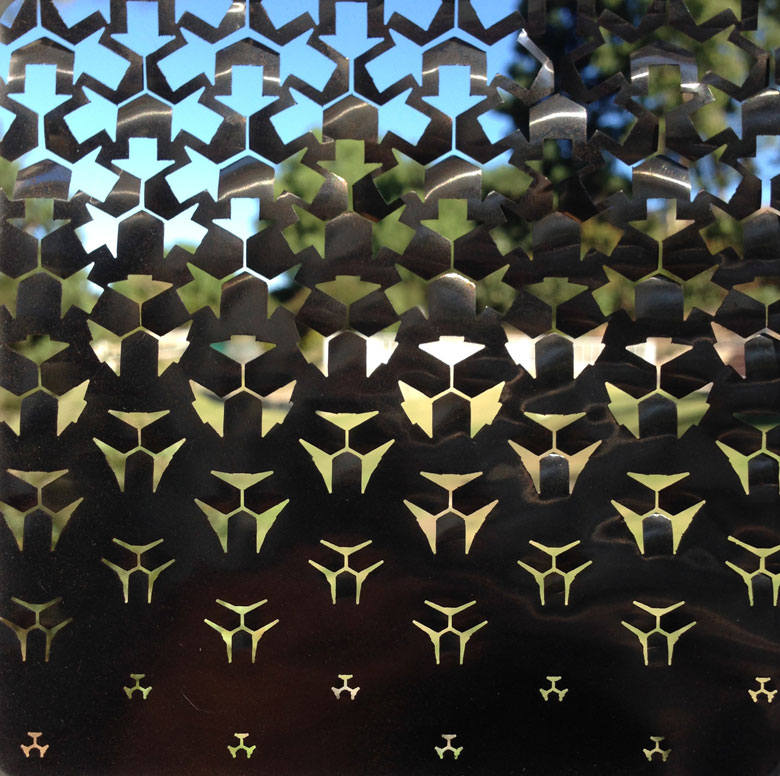
The architecture and research studio of Doris Sung, Dosu, has been exploring entirely passive adaptive shading components that require no additional energy input. These thermobimetal elements are thin laminations of two metals that expand and contract to heat at different rates. This causes them to either curl open when heated, providing ventilation, or to close due to the heat, controlling solar admission, depending on the desired strategy. The thermobimetals can be calibrated to operate at defined temperatures and to permit a certain degree of ventilation or light admission.

And similar to Paxton’s primitive evaporative cooling technique, new products incorporating Phase Change Materials (PCMs) can provide completely passive control over the transmission of heat into or out of an environment.
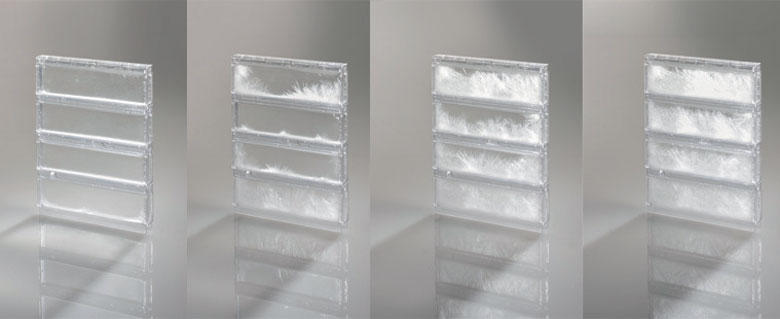
PCMs absorb excess internal and external heat and release it again as the temperature drops and heat is required. Products such as GlassX incorporate this technology into IGUs, employing translucent salt hydrates as the phase change material, hermetically sealed in clear polycarbonate.
While these units do not share the appearance of a typical, transparent, glazed window they can be employed more incongruously across an entirely glazed facade than other material elements, such as concrete or masonry walls, could. They offer a solution to the low thermal mass of glass – a prime benefit of concrete structures, stabilising internal and external temperature fluctuations – while also still permitting natural light through the facade. GlassX claim that for some buildings the requirement of powered heating or cooling can be completely eliminated.
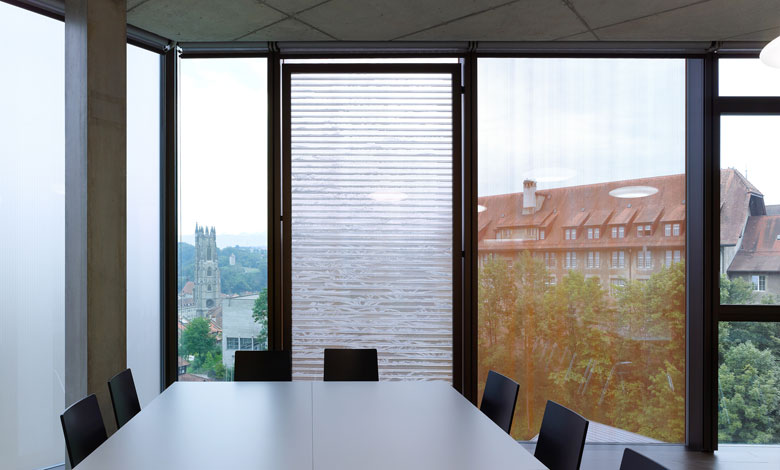
Clearly there are plenty of exciting technologies to be exploited and constraints to be tested in the attempt to capture the spirit of Paxton’s original Crystal Palace. It’s now up to the shortlist of architects to bring them together to create an iconic, pioneering building that may once again change our perspective of architectural space and its process of realisation.