Engineered nature: materials made to perform Brad Turner. November 13, 2015.
In this article, originally written for Architonic and re-published by Designboom, Materials Council explore the various ways that natural materials can be engineered, making them truly super-natural and offering entirely new methods of production and construction.
Man’s ability to engineer the natural materials of our environment into usable tools has come to define us throughout the ages. But while we have become increasingly skilled at creating utilitarian products from raw materials, we’ve also become more aware of the potential destructive ability of these processes and our actions on the environment.
We have now reached an age when this burden of responsibility and our advanced abilities to control and shape the materials around us have come together to create new products and manufacturing processes that are less synthetic creations, and more super-natural.
Here, we explore various examples of engineered nature that demonstrate the incredible level of control we can now exercise over our environment and how architects and designers can benefit from using products that are less synthetic in more ways than simply being more sustainable.
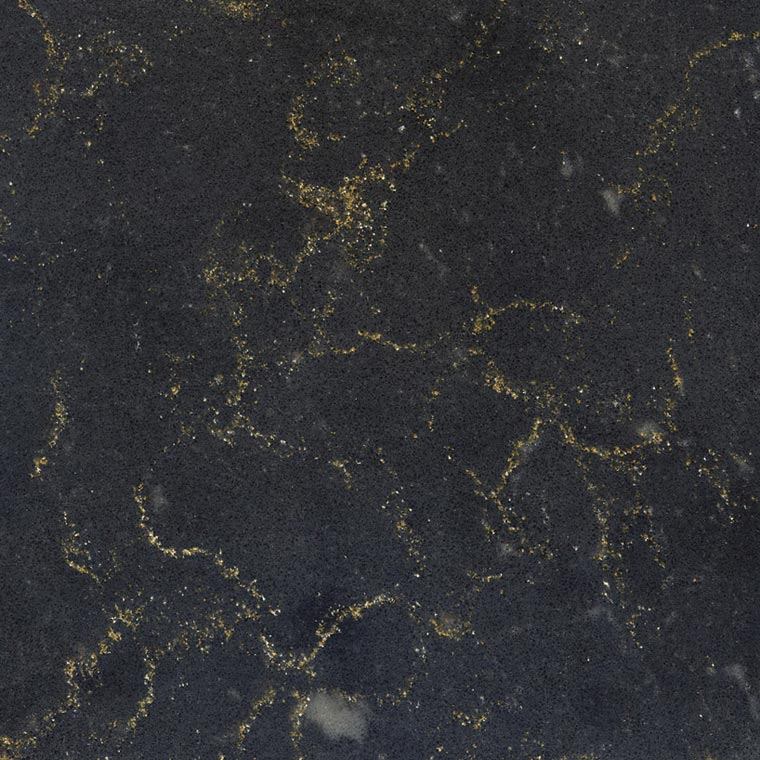
made of 94% natural quartz
Physical engineering
Reducing natural materials to their constituent elements, altering their make-up, and recombining them in new ways is an established method of enhancing the aesthetic and technical characteristics of a material. Reconstituted stone is perhaps the most common example of this, where waste from the quarrying of natural stones, such as marbles and granites, is reconstructed and held together with a binder to create man-made stones with a controlled appearance and a performance superior to natural stones.
With new manufacturing techniques, processes and the introduction of sophisticated computer control, manufacturers have also developed new and cost effective ways to also engineer the surfaces of natural materials. Lithos Design employ computer-modelling and 5-axis CNC (computer numerically controlled) machining of natural stone to create tessellating 3D-stone surfaces (top image), modular partitions and cladding panels for interiors. Traditionally extremely time consuming and highly-skilled work, hand-carved by stone masons.
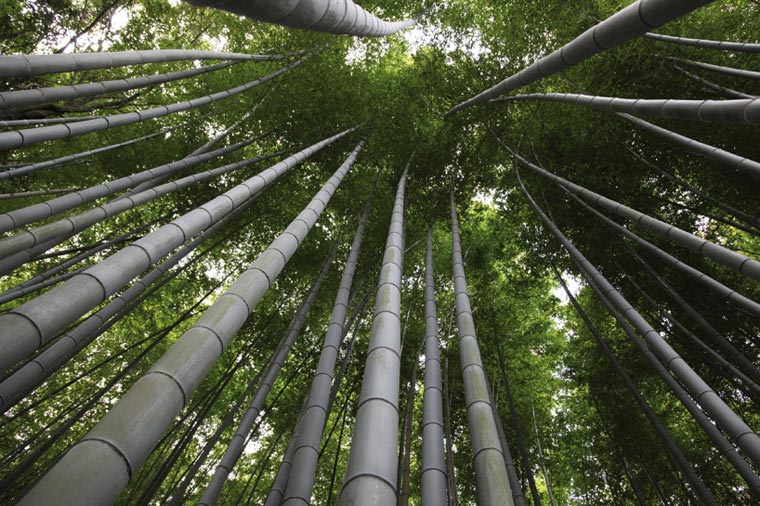
Some natural materials have inherent desirable performance and aesthetic qualities, yet their suitability for various applications and uses can be considerably restricted by their naturally occurring form. Bamboo is a rapidly renewable natural material, growing up to 1 metre each day, making it very sustainable for use in construction. But its naturally occurring hollow stem form does not lend itself well as a direct replacement for standardised timber products.
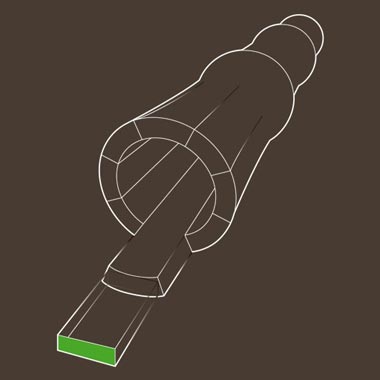
Manufacturers, such as Moso from the Netherlands, now produce bamboo in a range of standardised panels, boards, veneers and blocks, comparable to commonly available timber formats. These products are similar in appearance and performance to many hardwoods often used in architecture and design, if not surpassing them. Through a ‘carbonisation’ process of the naturally occurring sugars within bamboo, its appearance can also be altered from its natural straw yellow, through a range of darker tones, down to a rich colour similar to mahogany.
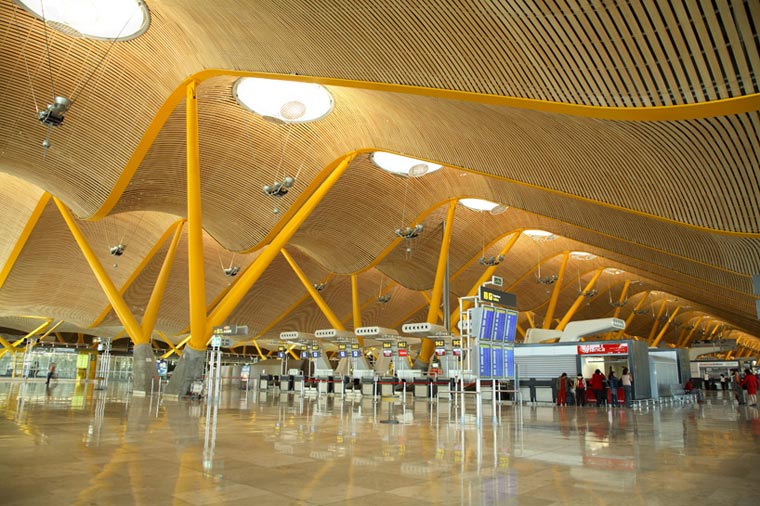
But we are no longer only restricted to homogenous materials, and in fact the concept of ‘engineered materials’ (materials designed to meet specific performance requirements) is most closely associated with composites. So it is appropriate that, in the world of engineered natural materials, composites are also prominent.
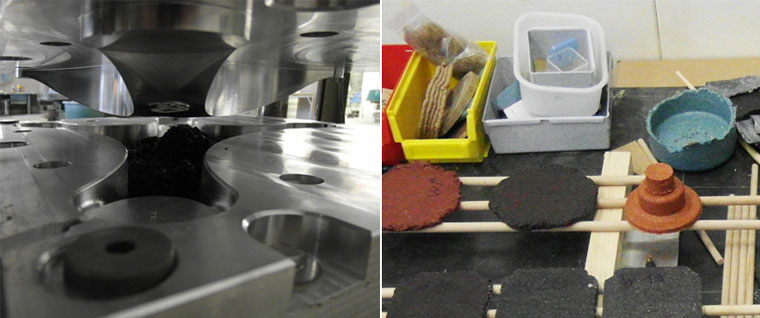
Zürich-based designer Beat Karrer is one of many designers to create a composite material manufactured from natural agricultural waste or by-products. His ‘Fluid Solids‘ material can be processed, formed and coloured using some of the same techniques as thermoplastics, providing a diverse range of opportunities for batch and mass-produced items, as demonstrated in the Architonic Concept Space unveiled at Milan 2012. Using an organic binding agent, his ‘Fluid Solids’ material is free from odours, toxins and is fully biodegradable, unlike synthetic composites, which are notoriously difficult to separate and recycle.
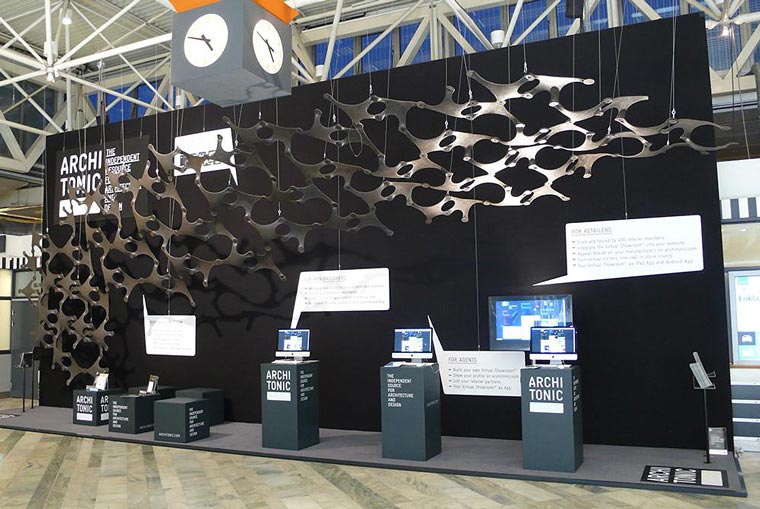
Chemical engineering
Beyond physically modifying the make-up, structure and form of natural materials, manufacturers are also able to chemically alter materials at the molecular level, allowing them to take what may be considered inferior or flawed materials and impart them with more beneficial performance characteristics.
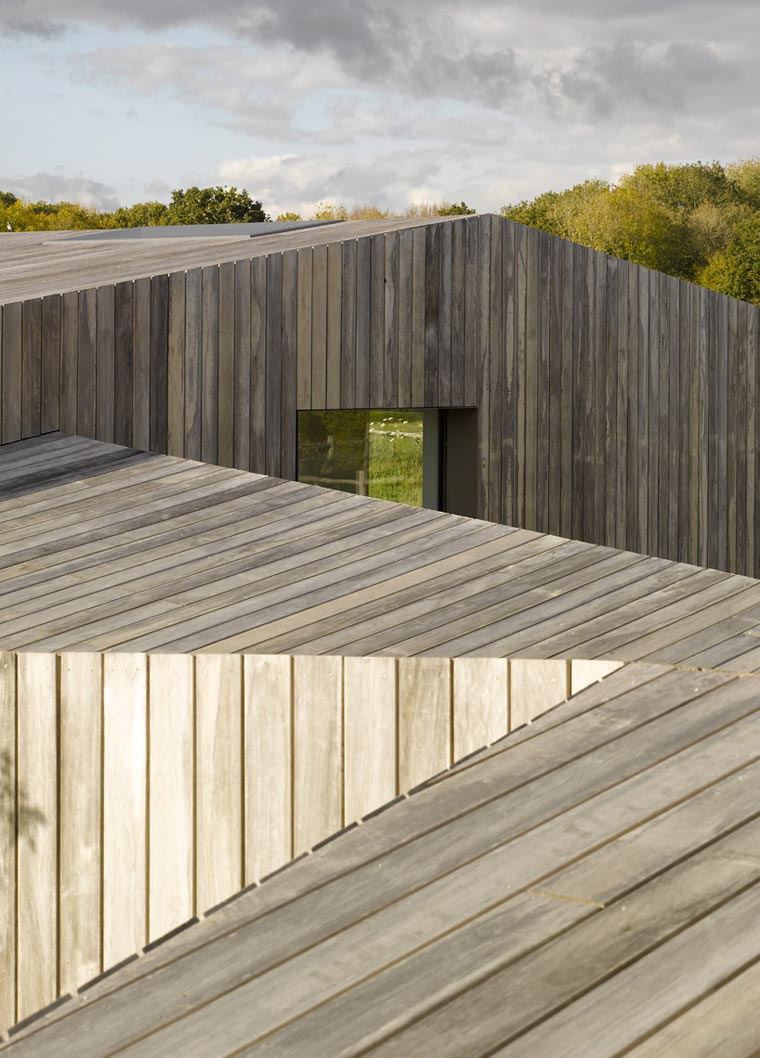
A new market of modified timber products (such as Platowood, Thermowood, Accoya and the recently created Kebony) employ various chemical-engineering techniques to radically improve the performance of certain timbers, providing a viable and sustainable alternative to slow-growing tropical hardwoods.
Kebony’s proprietary treatment process, Kebonization, impregnates a timber with liquid ‘biowastes’ to permanently modify the structure of its cell walls. This process produces timbers that are long-lasting, maintenance-free, dimensionally stable, resistant to fungal and insect-related degradation, hard-wearing and non-toxic. A side effect of Kebonization is the deepening of the timber’s colour tone, resulting in a rich chocolate brown, even in pale-toned timbers.
Kebonization is a polymerisation process, though not of products extracted from crude oil, as in traditional plastics, but from furfuryl alcohol, which is produced from agricultural crop waste. This creates the bio-polymer Furan, which strengthens the internal cell structure of the timber, giving Kebony its mechanical properties.
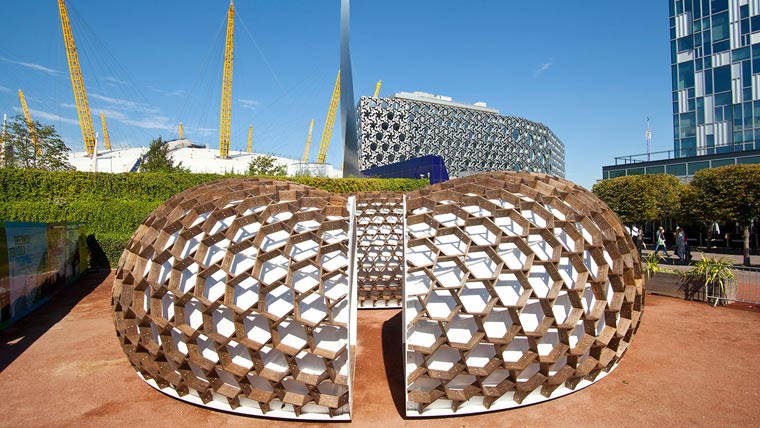
Bio-polymers, materials produced by or from living organisms, are also materials used in architecture and design in their own right, most commonly encountered in packaging. By reinforcing bio-polymers with natural fibres, engineers can create bio-composites usable on a much larger architectural scale as an alternative to conventional materials such as glass-fibre reinforced polymers. One such example is the ‘Learning from nature’ pavilion at Denmark’s Louisiana Museum of Modern Art, designed by 3XN, which won the JEC Innovation Award in 2010.
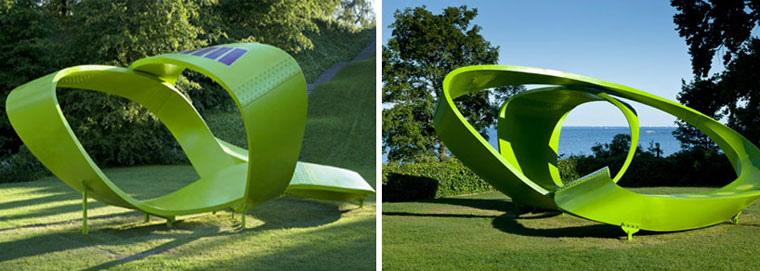
Growth and encouragement
We do not always have to apply brute strength to bend nature to our will. It is also possible to control or gently coerce it by exploiting inherent biological mechanisms such as growth or respiration. Green roofs, living facades and even urban farms are excellent examples of how it is possible to gently exercise control over nature for a specific purpose and as part of a larger architectural system.
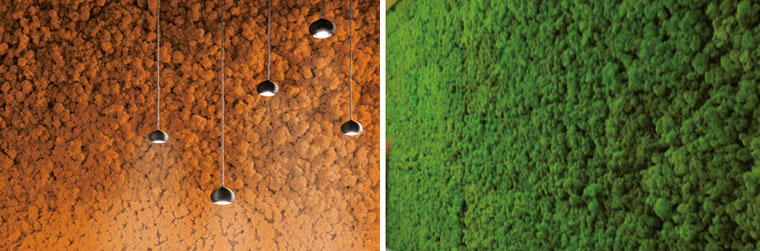
BenettiMOSS, by Benetti Stone, is such a product. A panelised interior vertical garden product composed of stabilised-lichen embedded in a resin base, BenettiMOSS regulates indoor moisture levels and cleanses the air of interiors. The lichen is extremely robust, requiring no irrigation, maintenance or even natural light to thrive.
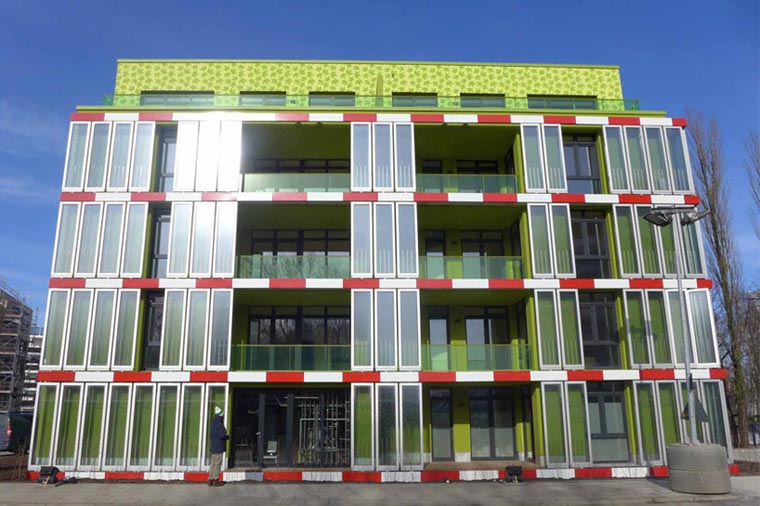
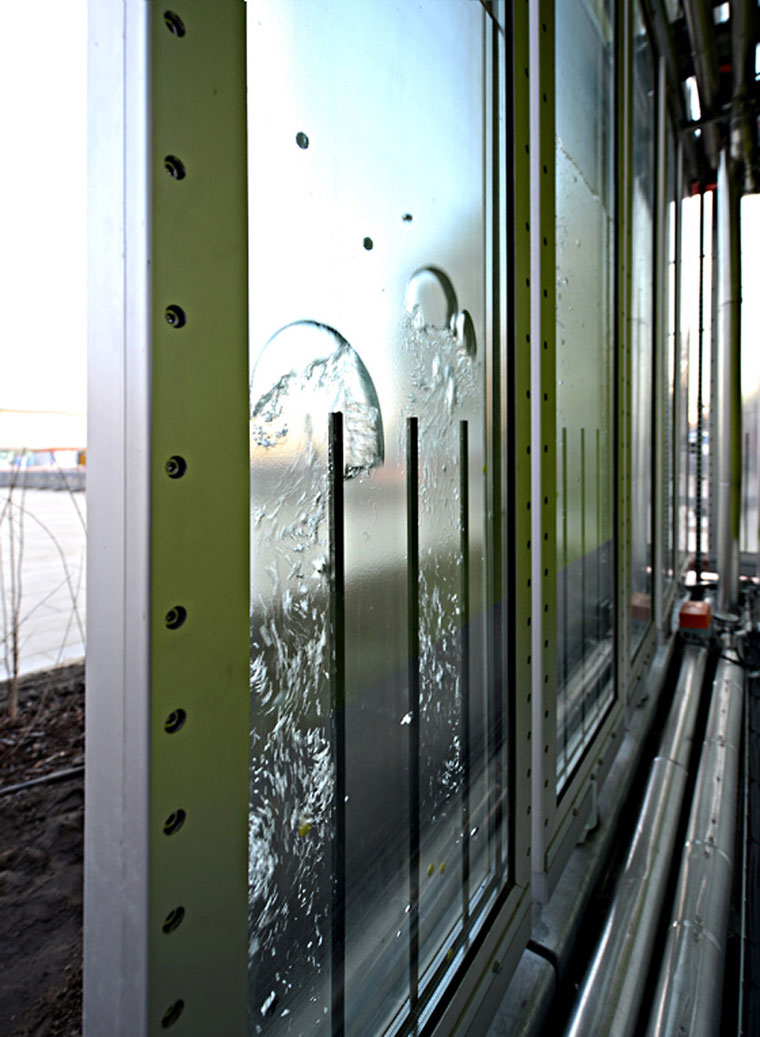
In April, international engineers Arup piloted a ‘bio-adaptive’ facade for the International Building Exhibition (IBA) in Hamburg. Housing live micro-algae in glazed facade elements, as it grows the algae provides adaptive solar shading, privacy, thermal insulation, noise reduction and also absorbs solar energy subsequently used to heat the building’s hot-water tank. The mature algae is then later harvested and fermented in an on-site biogas plant, producing usable energy.
This ability to coerce nature is no longer only being applied to producing materials or other products themselves, however, but also to propose entirely new manufacturing processes and techniques.
In addition to exploring the harnessing of nature’s energy, designer Markus Kayser has examined how to use it directly as a tool. In 2010 Kayser created a solar-powered laser-cutter that does not just capture solar energy to power a mechanical cutting tool, but channels the sun’s rays through a glass-ball lens to ‘laser’-cut 2D components. The following year, Kayser returned to the Egyptian desert, this time with his SolarSinter machine, which again makes use of solar rays to melt and reform the sand of the desert into solid objects, similar to the SLS (selective laser sintering) 3D-printing technique.
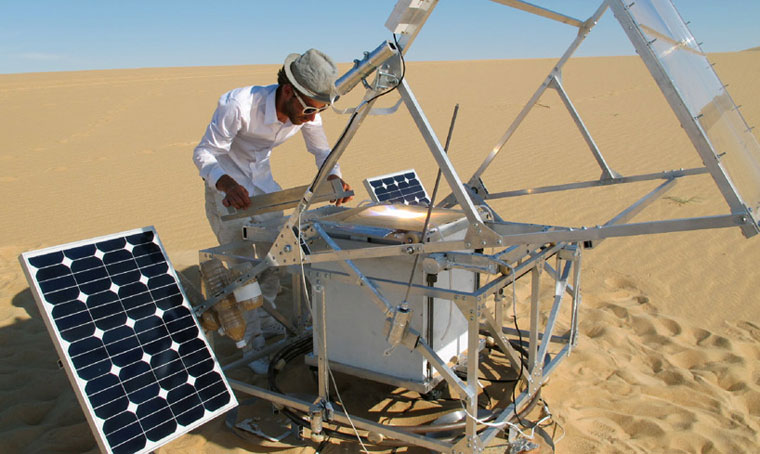
In 2008 London architect Magnus Larsson and Ordinary Ltd produced a study on how bacteria could be used to turn the sands of a desert into enormous sandstone structures, in effect an organic 3D-printer operating on an entirely new scale. This technique is most beneficial when building in difficult-to-access locations and environments, as the raw materials for construction do not have to be transported to site; the site itself is the material.
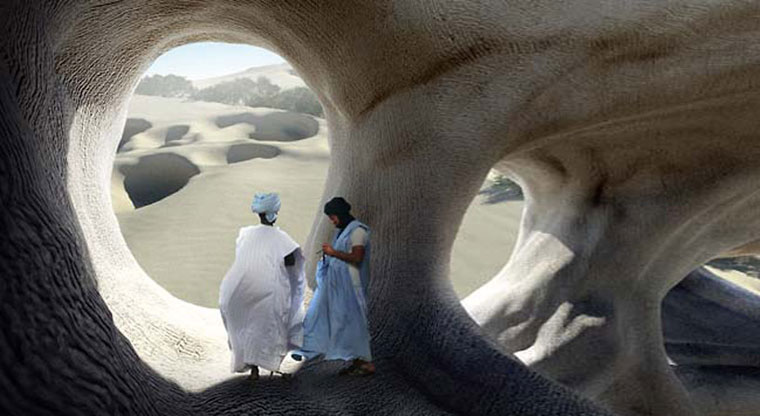
The sheer number of designers and manufacturers exploring similar ideas clearly demonstrates the belief in the benefits of this concept and its potential to revolutionise our future methods of construction. This is perhaps best envisioned by Foster + Partners‘ ambitious proposal to 3D-print large, moon-based structures from the lunar soil, using technology developed by D-Shape.
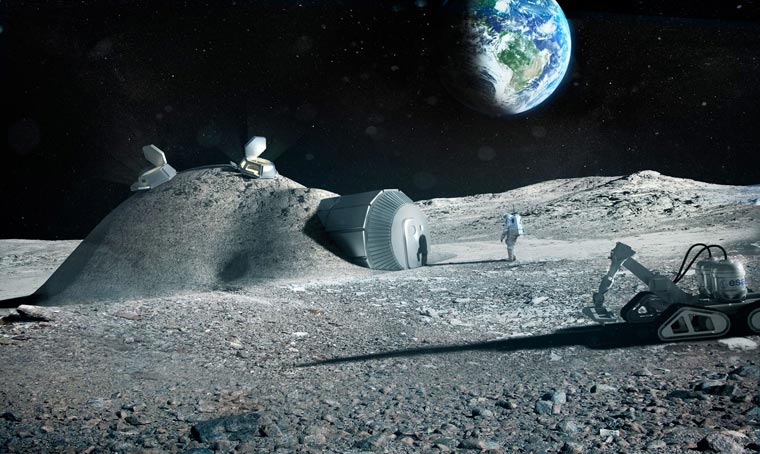
The examples of engineered nature discussed in this article show that by applying innovation and creative thinking to the more sustainable materials and resources available around us we are able to not only create attractive products that are more harmonious with our natural environment (while also performing as well, if not better, than established synthetic products), but we can also create entirely new models of production and construction, enabling us to extend the built environment beyond what we ever considered possible.