Mosa porcelain tiles production tour Brad Turner. December 7, 2015.
Materials Council visited the Maastricht facility of Mosa, The Netherlands’ last remaining porcelain tile manufacturer, to see first-hand the advanced production employed there. Founded in 1883, Mosa manufacture high quality, full-bodied porcelain wall and floor tiles with a design-led philosophy for the A&D market. Annually they produce over 6.5 million m2 of porcelain tiles and directly employ over 600 people.
Mosa’s relatively small production runs allow them to focus on high quality products and employ an experimental approach to product composition and surface design. Their unique Ultragres process for producing floor tiles delivers industry leading performance, achieving minimum porosity and maximum surface hardness. Mosa also offer custom designs and finishing techniques for projects of sufficient scale.
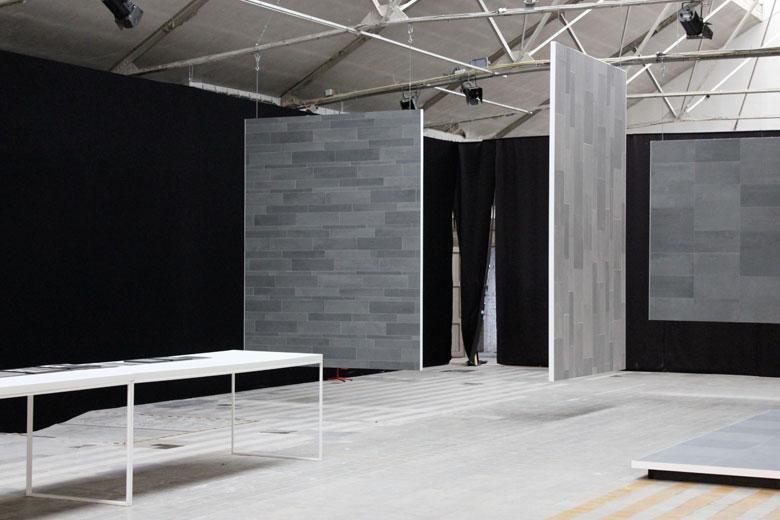
After a strategic realignment in the 1990s, Mosa decided to focus completely on the A&D community for all export markets, placing design at the core of the company’s philosophy. Since this cultural shift Mosa have instigated a program of high investment in new equipment, technology and techniques and employ a creative team of 10 designers and technicians focused solely on product innovation. Their approach of manufacturing on a standardised product base allows a high degree of flexibility in colouration and bespoke surface designs without fear of adversely affecting product performance.
With their focus on architecture and design professionals Mosa are exemplary in their provision of technical information, reference images and material samples. They are the world’s only Cradle to Cradle Certified ceramics manufacturer (awarded in 2011), and were early adopters of the system, having the first of their product lines certified in 2009.
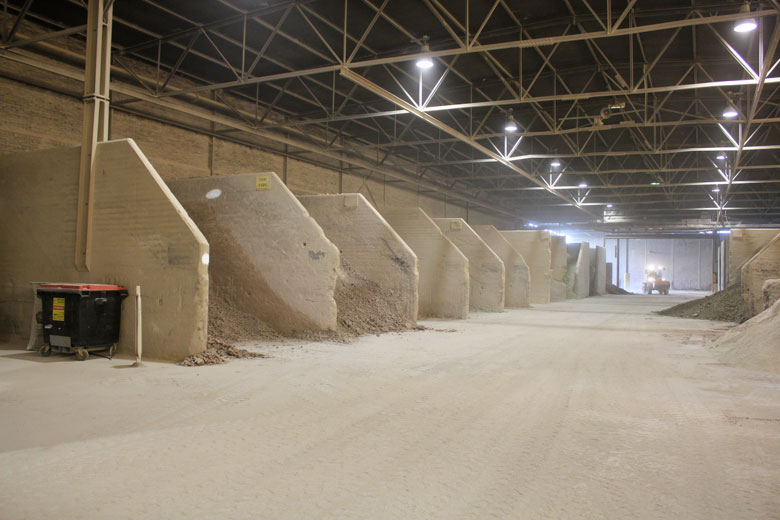
Production
At their manufacturing location in Maastricht, Mosa have separate facilities focused on their two main application areas: walls and floors. Both facilities employ a parallel process with slight variations, optimising the products for the requirements of their specific applications.
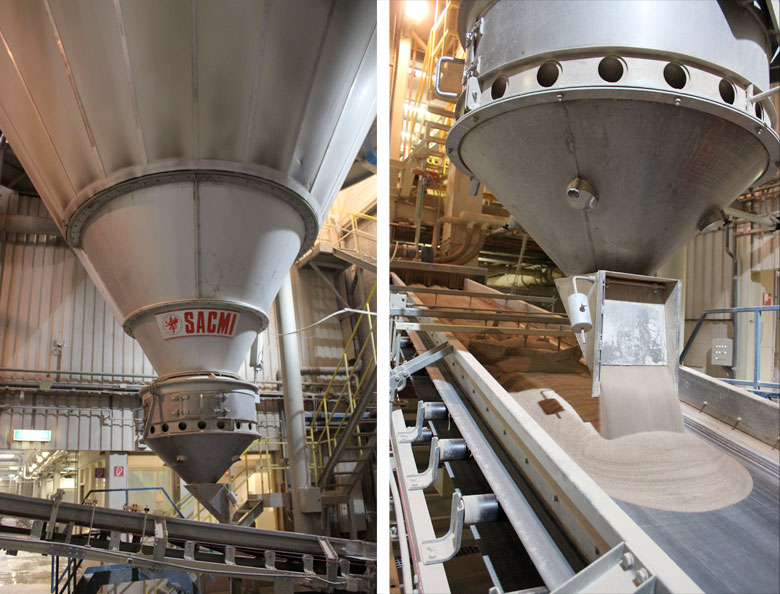
Production begins with the purchasing of high quality ingredients: clays, kaolin, quartz, magnesite and sand. Two inspections are carried out on the ingredients before being stored in the raw materials area. In line with Mosa’s environmental commitment, all raw ingredients are quarried within 450km of the production facility, minimising their energy consumption due to transportation while also supporting the region’s economy.
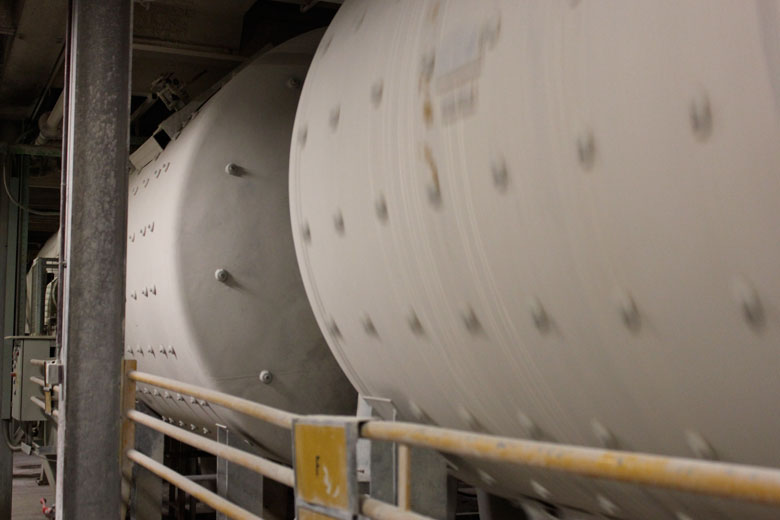
The raw materials are mixed and loaded into a 30m tall hopper that lays the ingredients onto a conveyor belt, delivering them into large drums used for further mixing and grinding. These steel drums contain 30mm porcelain balls, which, by rotating the drums, grind the ingredients into a fine powder over an 8-10 hour cycle.
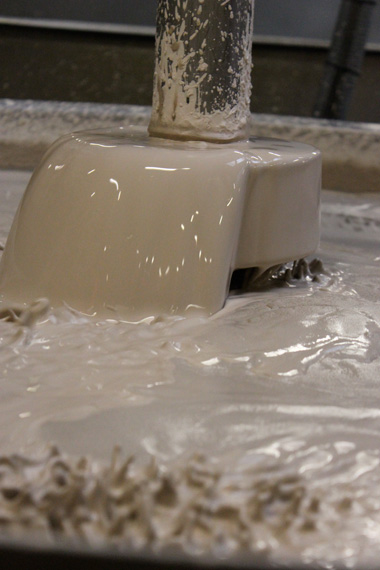
The freshly ground powder is mixed with wet clays into a slurry and stored in a vast lake directly beneath the factory floor. The slurry is sieved and vibrated, so that only particles of the correct size are taken to the next stage. The mixed and graded ingredients are then fed back into a heated hopper, drying them once more to a powder with the correct moisture content.
Pressing
The powdered ingredients are dropped onto a die, which gives each tile its overall shape, vibrated to remove any air bubbles and then pressed into a ‘green’ (an unfired tile). Pressing occurs at over 400 kgs/cm2, creating a dense and high strength product once fired. As the pressure must be applied uniformly across the tile, larger formats become increasingly challenging to produce to the required quality, as demonstrated by their increased price.
Mosa’s current maximum capabilities are 60 x 120 cm or 90 x 90 cm formats, with the intention to increase this further in the near future.
All Mosa’s products use the same standardised base composition, combined with pre-mixed batches of minerals and pigments, to allow speed and flexibility in producing different surfaces or ranges.
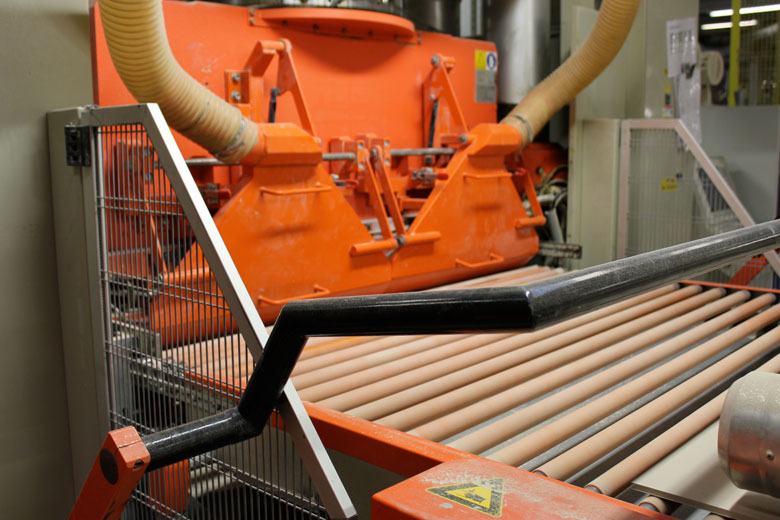
During the pressing stage Mosa employ their proprietary Ultragres technology for floor tiles, a system that produces an ultra hard, ultra low porosity 3mm wear layer. A layer of finely ground powder is dropped on top of the base mixture then pressed together into a unified product. This powder drop technique introduces variation to the appearance of the wear layer, ensuring the tiles share common characteristics yet each is unique, similar to products that display natural variation.
The unfired ‘greens’ are collected on ‘roller boxes’, each holding approximately 200 m2 of tiles, and transported to the next stage of the production by Mosa’s ‘TGV’ autonomous transportation units.
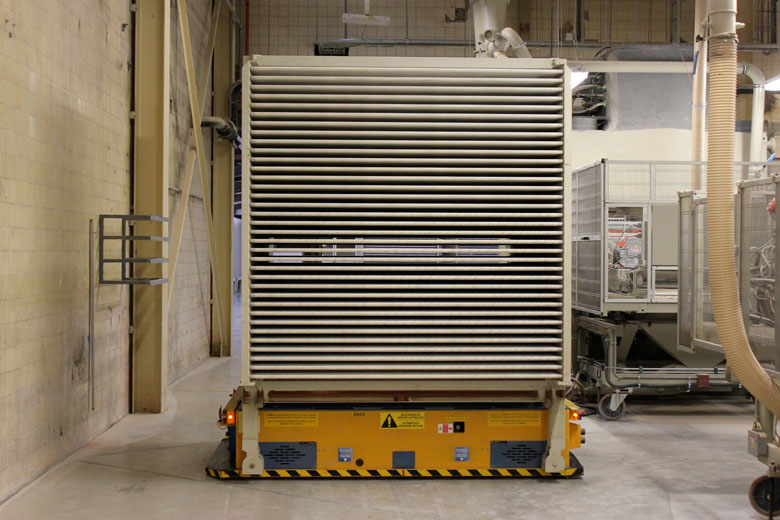
Firing
Firing is the next operation in production, where the ‘greens’ metamorphose into hard and high strength porcelain tiles. As a consequence of when their equipment was purchased, Mosa employ two kiln types in firing: traditional brick kilns and a modern conveyor ‘mono-fire’ kiln.
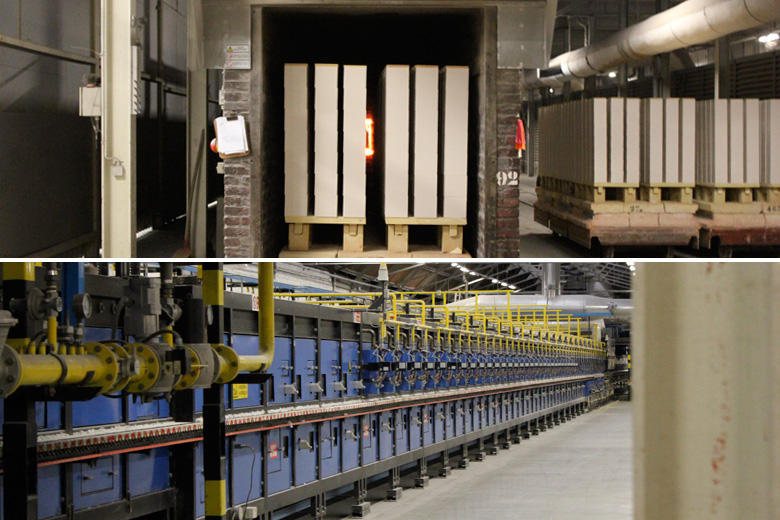
In the brick kiln 60m2 of tiles are stacked onto trolleys and gradually passed through the kiln over a period of 2-3 days. The brick kilns are primarily used for producing Mosa’s small format tiles, which can fall between the rollers of a modern kiln. Recovery of dropped tiles and kiln maintenance can be dangerous and difficult, exacerbated by the fact the kiln itself can never be switched off, Mosa’s oldest kiln has been in continuous operation since 1963.
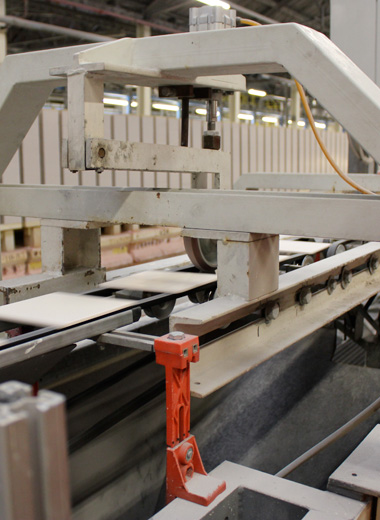
The modern kilns operate a process of ‘mono-firing’ where the tiles are stacked individually and gradually moved through the kilns, experiencing a precisely controlled temperature cycle. Firing occurs over a period of 45 – 80 minutes, reducing firing times by a factor of over x50 in comparison to traditional kilns. The kilns are gas fired, reaching peak temperatures of 1220oC.
Each tile size has a specific heating and cooling curve, requiring the kilns to be re-calibrated each time the format size being produced is changed. To minimise this disruption, runs of 4000m2 are produced before changing formats.
Following firing the tiles are fed onto a conveyor belt for quality control. A wheel applies pressure to the tile surface, cracking the tiles with imperfections and removing them from the production line to be collected for later recycling.
Glazed wall tiles are passed through a waterfall of liquid glaze, which is applied in a two stage process to ensure consistent coverage. Any prints and textures are subsequently roll-applied onto the wet glaze and the tiles are sent back for the second firing phase.
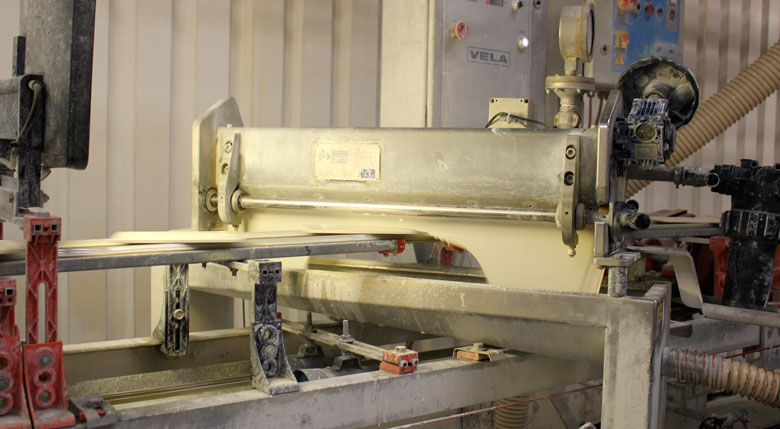
Once cooled the tiles are rectified, ensuring the edges are perfectly squared and the tile’s dimensions exact, and a micro-bevel is added to the edge using diamond-tipped tools. Rectification is carried out on all tiles larger than 45 x 45 cm. This is a necessary process as the pressed ‘greens’ are manufactured larger than necessary to accommodate the shrinkage that occurs during firing.
The micro-bevel is added to increases the longevity of the product by minimising the risk of spalling, the process whereby the vulnerable sharp corner formed between tile surface and edge chips through wear and tear.
The finished tiles are once more inspected for visual quality and imperfections before being packaged and stored for distribution. Their strict attention to quality control has led Mosa to achieve design tolerances 50% better than the requirements of British standards.
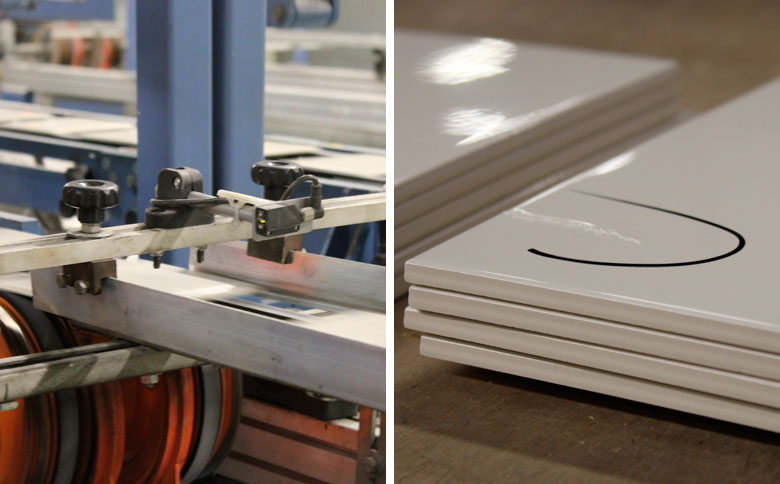
MAC – Mosa Architectural Centre
Our factory tour was concluded with a visit to the most recent addition to the production facility: the Mosa Architecture Centre or “MAC”. The MAC is a purpose-built showroom, allowing A&D professionals to view the finished products in all formats, forms and finishes within an ideal setting.
This is also an area where Mosa’s creative team experiment with ideas and combinations of products in staged settings, allowing visitors to walk amongst the Mosa catalogue.
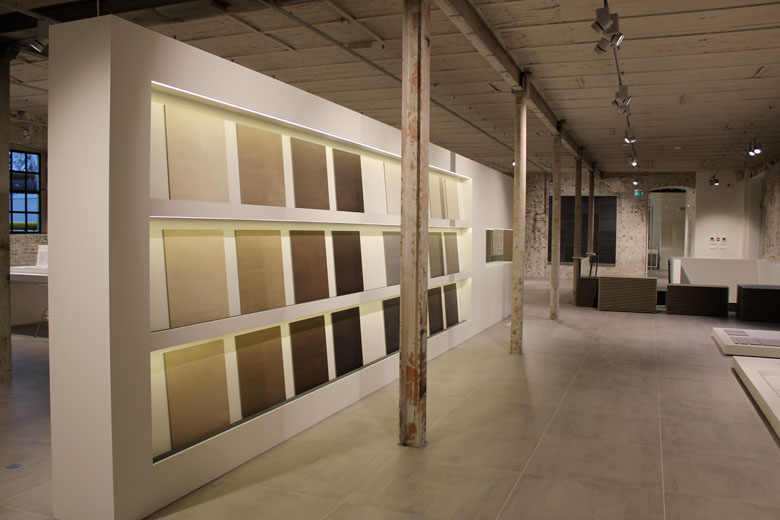
Performance data overview
Products:
• interior wall tiles
• floor tiles
• slip resistant tiles
• special pieces
• facade tiles (rainscreen)
• exterior flooring system
• Mosa LED (embedded LEDs)
• shower drains
Material construction:
• clays
• quartz
• feldspar
• kaolin
All sourced within 450 km of Maastricht production facility.
Available formats:
• 15 x 15 / 30 x 30 / 45 x 45 / 60 x 60 / 75 x 75 / 90 x 90 cm
• 10 x 30 / 15 x 30 / 5 x 60 / 10 x 60 / 15 x 60 / 60 x 90 / 60 x 120 cm
Other formats are also available.
• 100+ available colours
• customisable colours, finishes and formats available, minimum order applies
Applications:
• hospitality
• offices
• retail
• cultural
• healthcare sector
• schools and institutions
• residential
Sustainability:
• all defect tiles and waste from within the factory is collected and reprocessed
• water is collected and recycled
• no harmful chemicals are emitted to water
• Cradle to Cradle Certified Silver
• Up to 45% recycled content
• EPDs available upon request
• Renewable energy used in production where possible
• No harmful emissions during use or disposal of products
• KOMO certified in line with Dutch soil quality decree
Environmental accreditation and management:
• EN ISO 14001
• EN ISO 9001
• CE marked
• Cradle to Cradle Certified Silver
• Contributes towards BREEAM and LEED environmental assessments
• Environmental product declarations offered